What Components and Modules Does the Thermistor Contain?
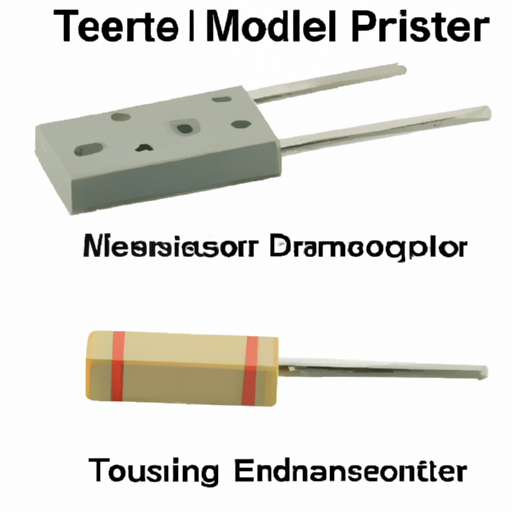
I. Introduction
Thermistors, a type of temperature sensor, play a crucial role in various applications, from consumer electronics to industrial processes. These devices are known for their sensitivity to temperature changes, making them essential for accurate temperature measurement and control. Understanding the components and modules that make up a thermistor is vital for anyone involved in electronics, engineering, or related fields. This blog post will explore the basic principles of thermistors, their key components, additional modules, applications, challenges, and future trends.
II. Basic Principles of Thermistors
A. Explanation of Thermistor Operation
Thermistors operate based on the principle that their resistance changes with temperature. This resistance-temperature relationship is highly nonlinear, which allows thermistors to be very sensitive to small changes in temperature.
1. **Resistance-Temperature Relationship**: The resistance of a thermistor decreases with an increase in temperature for Negative Temperature Coefficient (NTC) thermistors, while it increases for Positive Temperature Coefficient (PTC) thermistors. This characteristic makes NTC thermistors particularly useful for temperature sensing and control.
2. **Types of Thermistors**:
- **NTC Thermistors**: Commonly used for temperature measurement, NTC thermistors are made from semiconductor materials that exhibit a decrease in resistance as temperature rises.
- **PTC Thermistors**: These are often used for overcurrent protection and self-regulating heating applications, as their resistance increases with temperature.
B. Role of Materials in Thermistor Functionality
The materials used in thermistor construction significantly influence their performance. NTC thermistors are typically made from metal oxides, while PTC thermistors may use polymers or ceramic materials. The choice of materials affects the thermistor's sensitivity, response time, and temperature range.
III. Key Components of a Thermistor
A. Sensing Element
The sensing element is the heart of the thermistor, responsible for detecting temperature changes.
1. **Description of the Sensing Element**: The sensing element is usually a small bead or disk that changes resistance with temperature variations.
2. **Materials Used**: Common materials include metal oxides like manganese, nickel, and cobalt, which are sintered to form a ceramic structure. Polymers may also be used in PTC thermistors.
3. **Impact of Material Choice on Performance**: The specific composition and structure of the sensing element determine the thermistor's sensitivity, accuracy, and temperature range. For instance, a well-designed NTC thermistor can provide precise readings over a wide temperature range.
B. Encapsulation
Encapsulation protects the sensing element from environmental factors and mechanical damage.
1. **Purpose of Encapsulation**: It serves to shield the thermistor from moisture, dust, and other contaminants that could affect its performance.
2. **Common Materials Used for Encapsulation**: Epoxy resins and glass are frequently used for encapsulation. Epoxy provides good mechanical protection, while glass offers excellent thermal stability.
3. **Influence of Encapsulation on Thermistor Response Time and Durability**: The choice of encapsulation material can impact the thermistor's response time. For example, a thermistor with a thin epoxy coating may respond faster to temperature changes than one with a thicker glass encapsulation.
C. Leads and Terminals
Leads and terminals are essential for connecting the thermistor to a circuit.
1. **Types of Leads**: Thermistors can have various lead configurations, including wire leads for through-hole mounting and surface mount technology (SMT) for compact designs.
2. **Importance of Lead Configuration in Circuit Integration**: The lead configuration affects how easily the thermistor can be integrated into a circuit, influencing both design and performance.
3. **Connection Methods and Their Implications for Performance**: Different connection methods, such as soldering or using connectors, can impact the thermistor's reliability and accuracy. Proper connections are crucial for maintaining signal integrity.
IV. Additional Modules and Features
A. Temperature Compensation Circuits
Temperature compensation circuits are designed to enhance the accuracy of thermistor readings.
1. **Purpose and Function of Compensation Circuits**: These circuits adjust the output signal to account for non-linearities in the thermistor's response, ensuring more accurate temperature readings.
2. **Common Designs and Configurations**: Compensation circuits can be implemented using operational amplifiers or digital signal processors, depending on the application requirements.
B. Signal Conditioning Modules
Signal conditioning is essential for processing the raw output from thermistors.
1. **Importance of Signal Conditioning in Thermistor Applications**: Raw thermistor signals can be noisy and require conditioning to improve accuracy and reliability.
2. **Types of Signal Conditioning**: Common techniques include amplification to increase signal strength and filtering to remove noise. These processes ensure that the output signal is suitable for further processing or display.
C. Calibration and Testing Modules
Calibration is critical for ensuring that thermistors provide accurate temperature readings.
1. **Importance of Calibration for Accurate Temperature Readings**: Regular calibration helps maintain the accuracy of thermistors, especially in precision applications.
2. **Methods and Tools Used for Calibration**: Calibration can be performed using reference temperature sources and specialized equipment, such as thermocouples or calibrated temperature baths.
V. Applications of Thermistors
Thermistors are widely used across various industries due to their reliability and accuracy.
A. Consumer Electronics
In consumer electronics, thermistors are commonly used for temperature monitoring and control in devices like refrigerators, air conditioners, and ovens. They help maintain optimal operating conditions and improve energy efficiency.
B. Automotive Industry
In the automotive sector, thermistors are integral to engine temperature sensors and climate control systems. They provide critical data for engine management systems, ensuring optimal performance and safety.
C. Medical Devices
Thermistors are vital in medical devices, particularly in patient monitoring systems. They provide accurate temperature readings, which are essential for diagnosing and managing various health conditions.
D. Industrial Applications
In industrial settings, thermistors are used for process control and automation. They monitor temperatures in manufacturing processes, ensuring that equipment operates within safe limits and improving overall efficiency.
VI. Challenges and Considerations
A. Limitations of Thermistors
While thermistors are highly effective, they do have limitations.
1. **Temperature Range and Accuracy Issues**: Thermistors typically have a limited temperature range compared to other temperature sensors, such as thermocouples. Additionally, their non-linear response can complicate accurate readings.
B. Environmental Factors Affecting Performance
Environmental conditions can significantly impact thermistor performance.
1. **Humidity, Pressure, and Chemical Exposure**: High humidity, extreme pressure, and exposure to corrosive chemicals can affect the thermistor's accuracy and longevity. Proper encapsulation and material selection can mitigate these issues.
C. Future Trends in Thermistor Technology
1. **Advances in Materials and Design**: Ongoing research is focused on developing new materials and designs that enhance thermistor performance, such as improved sensitivity and wider temperature ranges. Innovations in nanotechnology and smart materials may lead to the next generation of thermistors.
VII. Conclusion
In summary, thermistors are complex devices composed of various components and modules that work together to provide accurate temperature measurements. Understanding these components—such as the sensing element, encapsulation, leads, and additional modules like temperature compensation and signal conditioning—is essential for anyone working with thermistors. As technology advances, the potential for thermistors to become even more accurate and versatile continues to grow, making them an indispensable tool in numerous applications.
VIII. References
For further reading on thermistors and their components, consider exploring the following resources:
1. "Thermistors: Theory and Applications" - Journal of Electronic Materials
2. "Temperature Sensors: A Comprehensive Guide" - Electronics Tutorials
3. "Advancements in Thermistor Technology" - IEEE Transactions on Industrial Electronics
By understanding the intricacies of thermistor design and functionality, engineers and technicians can better utilize these devices in their respective fields, ensuring optimal performance and reliability in temperature measurement and control applications.
What Components and Modules Does the Thermistor Contain?
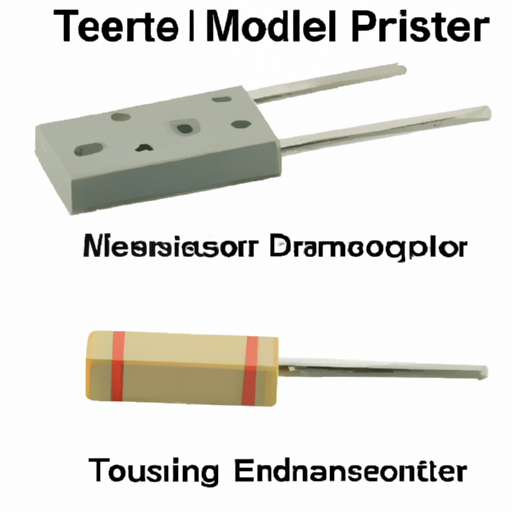
I. Introduction
Thermistors, a type of temperature sensor, play a crucial role in various applications, from consumer electronics to industrial processes. These devices are known for their sensitivity to temperature changes, making them essential for accurate temperature measurement and control. Understanding the components and modules that make up a thermistor is vital for anyone involved in electronics, engineering, or related fields. This blog post will explore the basic principles of thermistors, their key components, additional modules, applications, challenges, and future trends.
II. Basic Principles of Thermistors
A. Explanation of Thermistor Operation
Thermistors operate based on the principle that their resistance changes with temperature. This resistance-temperature relationship is highly nonlinear, which allows thermistors to be very sensitive to small changes in temperature.
1. **Resistance-Temperature Relationship**: The resistance of a thermistor decreases with an increase in temperature for Negative Temperature Coefficient (NTC) thermistors, while it increases for Positive Temperature Coefficient (PTC) thermistors. This characteristic makes NTC thermistors particularly useful for temperature sensing and control.
2. **Types of Thermistors**:
- **NTC Thermistors**: Commonly used for temperature measurement, NTC thermistors are made from semiconductor materials that exhibit a decrease in resistance as temperature rises.
- **PTC Thermistors**: These are often used for overcurrent protection and self-regulating heating applications, as their resistance increases with temperature.
B. Role of Materials in Thermistor Functionality
The materials used in thermistor construction significantly influence their performance. NTC thermistors are typically made from metal oxides, while PTC thermistors may use polymers or ceramic materials. The choice of materials affects the thermistor's sensitivity, response time, and temperature range.
III. Key Components of a Thermistor
A. Sensing Element
The sensing element is the heart of the thermistor, responsible for detecting temperature changes.
1. **Description of the Sensing Element**: The sensing element is usually a small bead or disk that changes resistance with temperature variations.
2. **Materials Used**: Common materials include metal oxides like manganese, nickel, and cobalt, which are sintered to form a ceramic structure. Polymers may also be used in PTC thermistors.
3. **Impact of Material Choice on Performance**: The specific composition and structure of the sensing element determine the thermistor's sensitivity, accuracy, and temperature range. For instance, a well-designed NTC thermistor can provide precise readings over a wide temperature range.
B. Encapsulation
Encapsulation protects the sensing element from environmental factors and mechanical damage.
1. **Purpose of Encapsulation**: It serves to shield the thermistor from moisture, dust, and other contaminants that could affect its performance.
2. **Common Materials Used for Encapsulation**: Epoxy resins and glass are frequently used for encapsulation. Epoxy provides good mechanical protection, while glass offers excellent thermal stability.
3. **Influence of Encapsulation on Thermistor Response Time and Durability**: The choice of encapsulation material can impact the thermistor's response time. For example, a thermistor with a thin epoxy coating may respond faster to temperature changes than one with a thicker glass encapsulation.
C. Leads and Terminals
Leads and terminals are essential for connecting the thermistor to a circuit.
1. **Types of Leads**: Thermistors can have various lead configurations, including wire leads for through-hole mounting and surface mount technology (SMT) for compact designs.
2. **Importance of Lead Configuration in Circuit Integration**: The lead configuration affects how easily the thermistor can be integrated into a circuit, influencing both design and performance.
3. **Connection Methods and Their Implications for Performance**: Different connection methods, such as soldering or using connectors, can impact the thermistor's reliability and accuracy. Proper connections are crucial for maintaining signal integrity.
IV. Additional Modules and Features
A. Temperature Compensation Circuits
Temperature compensation circuits are designed to enhance the accuracy of thermistor readings.
1. **Purpose and Function of Compensation Circuits**: These circuits adjust the output signal to account for non-linearities in the thermistor's response, ensuring more accurate temperature readings.
2. **Common Designs and Configurations**: Compensation circuits can be implemented using operational amplifiers or digital signal processors, depending on the application requirements.
B. Signal Conditioning Modules
Signal conditioning is essential for processing the raw output from thermistors.
1. **Importance of Signal Conditioning in Thermistor Applications**: Raw thermistor signals can be noisy and require conditioning to improve accuracy and reliability.
2. **Types of Signal Conditioning**: Common techniques include amplification to increase signal strength and filtering to remove noise. These processes ensure that the output signal is suitable for further processing or display.
C. Calibration and Testing Modules
Calibration is critical for ensuring that thermistors provide accurate temperature readings.
1. **Importance of Calibration for Accurate Temperature Readings**: Regular calibration helps maintain the accuracy of thermistors, especially in precision applications.
2. **Methods and Tools Used for Calibration**: Calibration can be performed using reference temperature sources and specialized equipment, such as thermocouples or calibrated temperature baths.
V. Applications of Thermistors
Thermistors are widely used across various industries due to their reliability and accuracy.
A. Consumer Electronics
In consumer electronics, thermistors are commonly used for temperature monitoring and control in devices like refrigerators, air conditioners, and ovens. They help maintain optimal operating conditions and improve energy efficiency.
B. Automotive Industry
In the automotive sector, thermistors are integral to engine temperature sensors and climate control systems. They provide critical data for engine management systems, ensuring optimal performance and safety.
C. Medical Devices
Thermistors are vital in medical devices, particularly in patient monitoring systems. They provide accurate temperature readings, which are essential for diagnosing and managing various health conditions.
D. Industrial Applications
In industrial settings, thermistors are used for process control and automation. They monitor temperatures in manufacturing processes, ensuring that equipment operates within safe limits and improving overall efficiency.
VI. Challenges and Considerations
A. Limitations of Thermistors
While thermistors are highly effective, they do have limitations.
1. **Temperature Range and Accuracy Issues**: Thermistors typically have a limited temperature range compared to other temperature sensors, such as thermocouples. Additionally, their non-linear response can complicate accurate readings.
B. Environmental Factors Affecting Performance
Environmental conditions can significantly impact thermistor performance.
1. **Humidity, Pressure, and Chemical Exposure**: High humidity, extreme pressure, and exposure to corrosive chemicals can affect the thermistor's accuracy and longevity. Proper encapsulation and material selection can mitigate these issues.
C. Future Trends in Thermistor Technology
1. **Advances in Materials and Design**: Ongoing research is focused on developing new materials and designs that enhance thermistor performance, such as improved sensitivity and wider temperature ranges. Innovations in nanotechnology and smart materials may lead to the next generation of thermistors.
VII. Conclusion
In summary, thermistors are complex devices composed of various components and modules that work together to provide accurate temperature measurements. Understanding these components—such as the sensing element, encapsulation, leads, and additional modules like temperature compensation and signal conditioning—is essential for anyone working with thermistors. As technology advances, the potential for thermistors to become even more accurate and versatile continues to grow, making them an indispensable tool in numerous applications.
VIII. References
For further reading on thermistors and their components, consider exploring the following resources:
1. "Thermistors: Theory and Applications" - Journal of Electronic Materials
2. "Temperature Sensors: A Comprehensive Guide" - Electronics Tutorials
3. "Advancements in Thermistor Technology" - IEEE Transactions on Industrial Electronics
By understanding the intricacies of thermistor design and functionality, engineers and technicians can better utilize these devices in their respective fields, ensuring optimal performance and reliability in temperature measurement and control applications.