Popular Models of Common Angle Heads
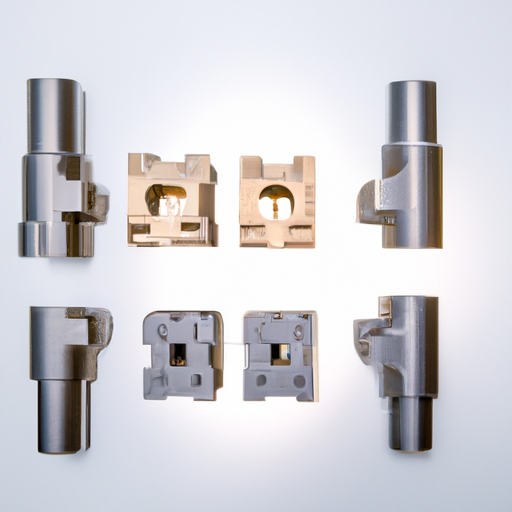
I. Introduction
In the world of machining and manufacturing, precision and versatility are paramount. One tool that embodies these qualities is the angle head. Angle heads are specialized attachments that allow machining operations to be performed at various angles, enhancing the capabilities of standard machines. This article aims to explore the significance of angle heads, delve into their features, and highlight some of the most popular models available in the market today.
II. Understanding Angle Heads
A. What are Angle Heads?
Angle heads are devices that attach to the spindle of a machine tool, enabling the cutting tool to operate at an angle to the spindle axis. This functionality allows for the machining of complex geometries and hard-to-reach areas without the need for repositioning the workpiece.
1. Description and Function
Angle heads can be fixed or adjustable. Fixed angle heads are set at a specific angle, typically 90 degrees, while adjustable angle heads allow for a range of angles, providing greater flexibility in machining operations.
2. Types of Angle Heads
Fixed Angle Heads: Best for repetitive tasks where the angle does not change.
Adjustable Angle Heads: Ideal for applications requiring various angles, such as contouring and complex part machining.
B. Applications of Angle Heads in Various Industries
Angle heads find applications across multiple industries, including:
1. Aerospace
In aerospace manufacturing, precision is critical. Angle heads are used for drilling and milling complex components, such as wing structures and engine parts, where access is limited.
2. Automotive
The automotive industry utilizes angle heads for machining intricate parts, such as engine blocks and transmission housings, where space constraints and precision are essential.
3. Medical Devices
Angle heads are employed in the production of medical devices, where precision machining is crucial for components like surgical instruments and implants.
4. General Manufacturing
In general manufacturing, angle heads enhance productivity by allowing for multi-faceted machining operations, reducing the need for multiple setups.
III. Key Features of Angle Heads
A. Design and Construction
1. Materials Used
Angle heads are typically constructed from high-strength materials such as steel or aluminum, ensuring durability and resistance to wear.
2. Size and Weight Considerations
The size and weight of an angle head can affect the overall performance of the machine. Lightweight designs are preferred for high-speed applications, while heavier models may be more suitable for robust machining tasks.
B. Performance Characteristics
1. Speed and Torque
Angle heads are designed to deliver high-speed performance while maintaining adequate torque for various machining tasks. This balance is crucial for achieving optimal results.
2. Precision and Accuracy
The precision of an angle head is determined by its design and construction. High-quality angle heads can achieve tolerances of a few microns, making them suitable for demanding applications.
C. Compatibility with Different Machines
1. CNC Machines
Most angle heads are compatible with CNC machines, allowing for automated and precise machining operations.
2. Manual Lathes and Mills
Angle heads can also be used with manual lathes and mills, providing versatility for shops that utilize both types of equipment.
IV. Popular Models of Angle Heads
A. Model 1: HAAS Angle Head
1. Specifications
- Angle: 90 degrees
- Maximum RPM: 10,000
- Tool Holder: CAT 40
2. Key Features
The HAAS angle head is known for its robust construction and high-speed capabilities, making it ideal for precision machining tasks.
3. Applications and Industries
Commonly used in aerospace and automotive industries for drilling and milling operations.
B. Model 2: Koma Precision Angle Head
1. Specifications
- Angle: Adjustable from 0 to 90 degrees
- Maximum RPM: 8,000
- Tool Holder: BT 30
2. Key Features
This model features an adjustable angle mechanism, allowing for versatile machining applications.
3. Applications and Industries
Widely used in general manufacturing and medical device production.
C. Model 3: HSK Angle Head by BIG Kaiser
1. Specifications
- Angle: 90 degrees
- Maximum RPM: 12,000
- Tool Holder: HSK 63
2. Key Features
The HSK angle head is designed for high-speed machining, offering excellent rigidity and precision.
3. Applications and Industries
Ideal for high-speed machining in the aerospace and automotive sectors.
D. Model 4: HPI Angle Head
1. Specifications
- Angle: Fixed at 45 degrees
- Maximum RPM: 6,000
- Tool Holder: CAT 50
2. Key Features
The HPI angle head is designed for heavy-duty applications, providing high torque and stability.
3. Applications and Industries
Commonly used in heavy manufacturing and machining of large components.
E. Model 5: TOS Angle Head
1. Specifications
- Angle: Adjustable from 0 to 180 degrees
- Maximum RPM: 7,500
- Tool Holder: BT 40
2. Key Features
This model offers a wide range of adjustability, making it suitable for complex machining tasks.
3. Applications and Industries
Used in various industries, including automotive and general manufacturing.
V. Comparison of Popular Models
A. Performance Metrics
1. Speed
The HAAS and BIG Kaiser models lead in maximum RPM, making them suitable for high-speed applications.
2. Torque
The HPI angle head excels in torque, making it ideal for heavy-duty machining tasks.
3. Precision
All models offer high precision, but the HAAS and BIG Kaiser models are particularly noted for their tight tolerances.
B. Cost Analysis
1. Price Range of Models
Prices vary significantly, with basic models starting around $1,500 and high-end models exceeding $5,000.
2. Value for Money
Investing in a high-quality angle head can lead to increased productivity and reduced machining time, offering excellent value for money.
C. User Reviews and Feedback
1. Common Praises
Users often praise the precision and versatility of angle heads, noting their ability to enhance machining capabilities.
2. Notable Criticisms
Some users report challenges with compatibility and setup, particularly with adjustable models.
VI. Choosing the Right Angle Head
A. Factors to Consider
1. Type of Machining Tasks
Consider the specific machining tasks you will perform. Fixed angle heads are suitable for repetitive tasks, while adjustable heads offer versatility.
2. Machine Compatibility
Ensure the angle head is compatible with your existing machines to avoid compatibility issues.
3. Budget Constraints
Determine your budget and weigh the cost against the features and benefits of each model.
B. Recommendations for Different Applications
1. Best for High-Speed Machining
The BIG Kaiser HSK angle head is recommended for high-speed applications due to its RPM capabilities.
2. Best for Precision Work
The HAAS angle head is ideal for precision work, offering tight tolerances and high accuracy.
3. Best for Versatility
The Koma Precision angle head is the best choice for versatility, with its adjustable angle feature.
VII. Maintenance and Care for Angle Heads
A. Importance of Regular Maintenance
Regular maintenance is crucial for ensuring the longevity and performance of angle heads.
B. Common Maintenance Practices
1. Cleaning
Keep the angle head clean to prevent debris buildup that can affect performance.
2. Lubrication
Regular lubrication is essential for smooth operation and to reduce wear.
3. Inspection for Wear and Tear
Regularly inspect the angle head for signs of wear and tear, addressing any issues promptly.
C. Troubleshooting Common Issues
Common issues include misalignment and reduced performance, which can often be resolved through proper maintenance and adjustments.
VIII. Conclusion
Angle heads are invaluable tools in the machining and manufacturing industries, offering enhanced precision and versatility. By understanding the various models available and their applications, manufacturers can make informed decisions that optimize their machining processes. Regular maintenance and care are essential for ensuring the longevity and performance of these tools, ultimately leading to improved productivity and efficiency.
IX. References
- Manufacturer websites and product catalogs
- Industry publications and journals
- Technical manuals and user guides for angle heads
In conclusion, whether you are in aerospace, automotive, or general manufacturing, selecting the right angle head can significantly impact your machining capabilities. By considering the factors outlined in this article, you can choose an angle head that meets your specific needs and enhances your production processes.
Popular Models of Common Angle Heads
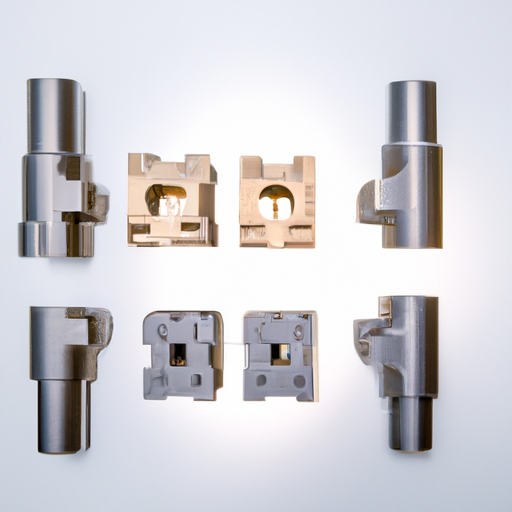
I. Introduction
In the world of machining and manufacturing, precision and versatility are paramount. One tool that embodies these qualities is the angle head. Angle heads are specialized attachments that allow machining operations to be performed at various angles, enhancing the capabilities of standard machines. This article aims to explore the significance of angle heads, delve into their features, and highlight some of the most popular models available in the market today.
II. Understanding Angle Heads
A. What are Angle Heads?
Angle heads are devices that attach to the spindle of a machine tool, enabling the cutting tool to operate at an angle to the spindle axis. This functionality allows for the machining of complex geometries and hard-to-reach areas without the need for repositioning the workpiece.
1. Description and Function
Angle heads can be fixed or adjustable. Fixed angle heads are set at a specific angle, typically 90 degrees, while adjustable angle heads allow for a range of angles, providing greater flexibility in machining operations.
2. Types of Angle Heads
Fixed Angle Heads: Best for repetitive tasks where the angle does not change.
Adjustable Angle Heads: Ideal for applications requiring various angles, such as contouring and complex part machining.
B. Applications of Angle Heads in Various Industries
Angle heads find applications across multiple industries, including:
1. Aerospace
In aerospace manufacturing, precision is critical. Angle heads are used for drilling and milling complex components, such as wing structures and engine parts, where access is limited.
2. Automotive
The automotive industry utilizes angle heads for machining intricate parts, such as engine blocks and transmission housings, where space constraints and precision are essential.
3. Medical Devices
Angle heads are employed in the production of medical devices, where precision machining is crucial for components like surgical instruments and implants.
4. General Manufacturing
In general manufacturing, angle heads enhance productivity by allowing for multi-faceted machining operations, reducing the need for multiple setups.
III. Key Features of Angle Heads
A. Design and Construction
1. Materials Used
Angle heads are typically constructed from high-strength materials such as steel or aluminum, ensuring durability and resistance to wear.
2. Size and Weight Considerations
The size and weight of an angle head can affect the overall performance of the machine. Lightweight designs are preferred for high-speed applications, while heavier models may be more suitable for robust machining tasks.
B. Performance Characteristics
1. Speed and Torque
Angle heads are designed to deliver high-speed performance while maintaining adequate torque for various machining tasks. This balance is crucial for achieving optimal results.
2. Precision and Accuracy
The precision of an angle head is determined by its design and construction. High-quality angle heads can achieve tolerances of a few microns, making them suitable for demanding applications.
C. Compatibility with Different Machines
1. CNC Machines
Most angle heads are compatible with CNC machines, allowing for automated and precise machining operations.
2. Manual Lathes and Mills
Angle heads can also be used with manual lathes and mills, providing versatility for shops that utilize both types of equipment.
IV. Popular Models of Angle Heads
A. Model 1: HAAS Angle Head
1. Specifications
- Angle: 90 degrees
- Maximum RPM: 10,000
- Tool Holder: CAT 40
2. Key Features
The HAAS angle head is known for its robust construction and high-speed capabilities, making it ideal for precision machining tasks.
3. Applications and Industries
Commonly used in aerospace and automotive industries for drilling and milling operations.
B. Model 2: Koma Precision Angle Head
1. Specifications
- Angle: Adjustable from 0 to 90 degrees
- Maximum RPM: 8,000
- Tool Holder: BT 30
2. Key Features
This model features an adjustable angle mechanism, allowing for versatile machining applications.
3. Applications and Industries
Widely used in general manufacturing and medical device production.
C. Model 3: HSK Angle Head by BIG Kaiser
1. Specifications
- Angle: 90 degrees
- Maximum RPM: 12,000
- Tool Holder: HSK 63
2. Key Features
The HSK angle head is designed for high-speed machining, offering excellent rigidity and precision.
3. Applications and Industries
Ideal for high-speed machining in the aerospace and automotive sectors.
D. Model 4: HPI Angle Head
1. Specifications
- Angle: Fixed at 45 degrees
- Maximum RPM: 6,000
- Tool Holder: CAT 50
2. Key Features
The HPI angle head is designed for heavy-duty applications, providing high torque and stability.
3. Applications and Industries
Commonly used in heavy manufacturing and machining of large components.
E. Model 5: TOS Angle Head
1. Specifications
- Angle: Adjustable from 0 to 180 degrees
- Maximum RPM: 7,500
- Tool Holder: BT 40
2. Key Features
This model offers a wide range of adjustability, making it suitable for complex machining tasks.
3. Applications and Industries
Used in various industries, including automotive and general manufacturing.
V. Comparison of Popular Models
A. Performance Metrics
1. Speed
The HAAS and BIG Kaiser models lead in maximum RPM, making them suitable for high-speed applications.
2. Torque
The HPI angle head excels in torque, making it ideal for heavy-duty machining tasks.
3. Precision
All models offer high precision, but the HAAS and BIG Kaiser models are particularly noted for their tight tolerances.
B. Cost Analysis
1. Price Range of Models
Prices vary significantly, with basic models starting around $1,500 and high-end models exceeding $5,000.
2. Value for Money
Investing in a high-quality angle head can lead to increased productivity and reduced machining time, offering excellent value for money.
C. User Reviews and Feedback
1. Common Praises
Users often praise the precision and versatility of angle heads, noting their ability to enhance machining capabilities.
2. Notable Criticisms
Some users report challenges with compatibility and setup, particularly with adjustable models.
VI. Choosing the Right Angle Head
A. Factors to Consider
1. Type of Machining Tasks
Consider the specific machining tasks you will perform. Fixed angle heads are suitable for repetitive tasks, while adjustable heads offer versatility.
2. Machine Compatibility
Ensure the angle head is compatible with your existing machines to avoid compatibility issues.
3. Budget Constraints
Determine your budget and weigh the cost against the features and benefits of each model.
B. Recommendations for Different Applications
1. Best for High-Speed Machining
The BIG Kaiser HSK angle head is recommended for high-speed applications due to its RPM capabilities.
2. Best for Precision Work
The HAAS angle head is ideal for precision work, offering tight tolerances and high accuracy.
3. Best for Versatility
The Koma Precision angle head is the best choice for versatility, with its adjustable angle feature.
VII. Maintenance and Care for Angle Heads
A. Importance of Regular Maintenance
Regular maintenance is crucial for ensuring the longevity and performance of angle heads.
B. Common Maintenance Practices
1. Cleaning
Keep the angle head clean to prevent debris buildup that can affect performance.
2. Lubrication
Regular lubrication is essential for smooth operation and to reduce wear.
3. Inspection for Wear and Tear
Regularly inspect the angle head for signs of wear and tear, addressing any issues promptly.
C. Troubleshooting Common Issues
Common issues include misalignment and reduced performance, which can often be resolved through proper maintenance and adjustments.
VIII. Conclusion
Angle heads are invaluable tools in the machining and manufacturing industries, offering enhanced precision and versatility. By understanding the various models available and their applications, manufacturers can make informed decisions that optimize their machining processes. Regular maintenance and care are essential for ensuring the longevity and performance of these tools, ultimately leading to improved productivity and efficiency.
IX. References
- Manufacturer websites and product catalogs
- Industry publications and journals
- Technical manuals and user guides for angle heads
In conclusion, whether you are in aerospace, automotive, or general manufacturing, selecting the right angle head can significantly impact your machining capabilities. By considering the factors outlined in this article, you can choose an angle head that meets your specific needs and enhances your production processes.