Common Production Processes for DC Resistors
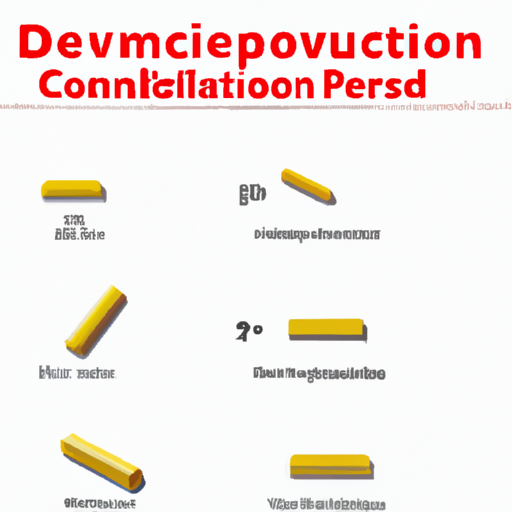
I. Introduction
A. Definition of DC Resistors
DC resistors are passive electronic components that resist the flow of direct current (DC) in a circuit. They are essential for controlling voltage and current levels, dividing voltages, and protecting sensitive components from excessive current. Resistors are characterized by their resistance value, which is measured in ohms (Ω), and they come in various types and configurations to suit different applications.
B. Importance of DC Resistors in Electronic Circuits
In electronic circuits, DC resistors play a crucial role in ensuring proper functionality. They are used in a wide range of applications, from simple circuits in household electronics to complex systems in industrial machinery. By managing current flow, resistors help maintain circuit stability, prevent damage to components, and ensure that devices operate within their specified parameters. Their reliability and performance are vital for the overall efficiency of electronic systems.
C. Overview of the Production Process
The production of DC resistors involves several key processes, from sourcing raw materials to final testing and packaging. Understanding these processes is essential for manufacturers aiming to produce high-quality resistors that meet industry standards. This blog post will explore the common production processes for DC resistors, including the types of resistors, raw materials used, fabrication techniques, and the impact of technology and environmental considerations.
II. Types of DC Resistors
A. Fixed Resistors
Fixed resistors have a constant resistance value and are the most commonly used type in electronic circuits. They can be further categorized into:
1. **Carbon Composition Resistors**: Made from a mixture of carbon and a binding material, these resistors are known for their high energy absorption and ability to withstand high temperatures.
2. **Metal Film Resistors**: These resistors are constructed by depositing a thin layer of metal onto a ceramic substrate. They offer high precision and stability, making them suitable for applications requiring accurate resistance values.
3. **Wirewound Resistors**: Composed of a wire wound around a core, these resistors can handle high power levels and are often used in power applications.
B. Variable Resistors
Variable resistors allow for adjustable resistance values, making them versatile components in electronic circuits. They include:
1. **Potentiometers**: Used for adjusting voltage levels in circuits, potentiometers are commonly found in volume controls and other adjustable settings.
2. **Rheostats**: Similar to potentiometers but designed to handle higher currents, rheostats are used in applications where variable resistance is needed.
C. Specialty Resistors
Specialty resistors are designed for specific applications and include:
1. **Precision Resistors**: These resistors have tight tolerance levels and are used in applications where accuracy is critical.
2. **High-Power Resistors**: Built to withstand high power levels, these resistors are used in industrial applications and power electronics.
III. Raw Materials Used in Resistor Production
A. Conductive Materials
The performance of resistors largely depends on the materials used in their construction. Common conductive materials include:
1. **Carbon**: Used in carbon composition resistors, carbon provides good conductivity and thermal stability.
2. **Metal Oxides**: Employed in metal film resistors, metal oxides offer high precision and stability.
3. **Metal Alloys**: Used in wirewound resistors, metal alloys provide durability and high power handling capabilities.
B. Insulating Materials
Insulating materials are crucial for ensuring the safety and reliability of resistors. Common insulating materials include:
1. **Ceramics**: Often used as substrates for resistors, ceramics provide excellent thermal and electrical insulation.
2. **Epoxy Resins**: Used for encapsulating resistors, epoxy resins protect against environmental factors and mechanical stress.
3. **Plastics**: Employed in various resistor types, plastics offer lightweight and cost-effective insulation solutions.
IV. Common Production Processes
A. Material Preparation
1. Sourcing and Quality Control
The production of DC resistors begins with sourcing high-quality raw materials. Manufacturers must establish relationships with reliable suppliers and implement stringent quality control measures to ensure that materials meet industry standards.
2. Material Processing Techniques
Once sourced, raw materials undergo processing techniques such as grinding, mixing, and shaping to prepare them for resistor fabrication. For example, carbon materials may be ground into a fine powder, while metal films are deposited onto substrates using advanced techniques.
B. Resistor Fabrication
The fabrication process varies depending on the type of resistor being produced:
1. Carbon Composition Resistors
Mixing and Molding: The carbon powder is mixed with a binding agent and molded into the desired shape.
Curing and Finishing: The molded resistors are cured to harden the material, followed by finishing processes to achieve the required resistance values.
2. Metal Film Resistors
Thin Film Deposition: A thin layer of metal is deposited onto a ceramic substrate using techniques such as sputtering or chemical vapor deposition.
Laser Trimming: The resistance value is fine-tuned using laser trimming, which removes precise amounts of the metal film.
3. Wirewound Resistors
Wire Winding: A wire is wound around a core to create the resistor element.
Insulation and Coating: The wound wire is insulated and coated to protect against environmental factors and ensure safety.
C. Assembly and Packaging
1. Mounting Techniques
After fabrication, resistors are mounted onto circuit boards using various techniques, including surface mount technology (SMT) and through-hole mounting.
2. Encapsulation and Coating
Resistors are encapsulated in protective materials to shield them from moisture, dust, and mechanical stress. This step is crucial for ensuring long-term reliability.
D. Testing and Quality Assurance
1. Electrical Testing
Each resistor undergoes electrical testing to verify its resistance value and performance characteristics. This step ensures that the resistors meet specified tolerances.
2. Environmental Testing
Resistors are subjected to environmental testing to assess their performance under various conditions, such as temperature and humidity.
3. Reliability Testing
Reliability testing evaluates the long-term performance of resistors, ensuring they can withstand the rigors of their intended applications.
V. Automation and Technology in Resistor Production
A. Role of Automation in Manufacturing
Automation plays a significant role in the production of DC resistors, enhancing efficiency and consistency. Automated systems streamline processes such as material handling, assembly, and testing, reducing the risk of human error.
B. Advances in Production Technology
Recent advancements in production technology, such as 3D printing and advanced material science, have opened new avenues for resistor design and manufacturing. These technologies enable the creation of more complex resistor structures and improved performance characteristics.
C. Impact of Industry 4.0 on Resistor Production
The integration of Industry 4.0 principles, including the Internet of Things (IoT) and data analytics, is transforming resistor production. Manufacturers can now monitor production processes in real-time, optimize operations, and enhance product quality through data-driven decision-making.
VI. Environmental Considerations
A. Sustainable Practices in Resistor Manufacturing
As environmental concerns grow, manufacturers are adopting sustainable practices in resistor production. This includes using eco-friendly materials, reducing energy consumption, and minimizing waste.
B. Waste Management and Recycling
Effective waste management strategies are essential for reducing the environmental impact of resistor production. Manufacturers are implementing recycling programs to reclaim materials and reduce landfill waste.
C. Compliance with Environmental Regulations
Compliance with environmental regulations is crucial for resistor manufacturers. Adhering to standards ensures that production processes are environmentally responsible and sustainable.
VII. Conclusion
A. Summary of Key Points
The production of DC resistors involves a complex interplay of materials, fabrication techniques, and quality assurance processes. Understanding these processes is essential for manufacturers aiming to produce reliable and high-performance resistors.
B. Future Trends in DC Resistor Production
As technology continues to evolve, the future of DC resistor production will likely see further advancements in automation, material science, and sustainable practices. Manufacturers must stay abreast of these trends to remain competitive in the market.
C. Importance of Continuous Improvement in Manufacturing Processes
Continuous improvement is vital for enhancing the quality and efficiency of resistor production. By embracing innovation and adopting best practices, manufacturers can ensure that they meet the ever-changing demands of the electronics industry.
VIII. References
A. Academic Journals
- Journal of Electronic Materials
- IEEE Transactions on Components, Packaging and Manufacturing Technology
B. Industry Reports
- Market Research Reports on Resistor Manufacturing
- Industry Analysis Reports from Electronics Associations
C. Manufacturer Guidelines
- Technical Specifications from Resistor Manufacturers
- Best Practices for Resistor Production from Industry Leaders
---
This blog post provides a comprehensive overview of the common production processes for DC resistors, highlighting the importance of these components in electronic circuits and the various factors that influence their manufacturing. By understanding these processes, manufacturers can enhance their production capabilities and contribute to the advancement of electronic technology.
Common Production Processes for DC Resistors
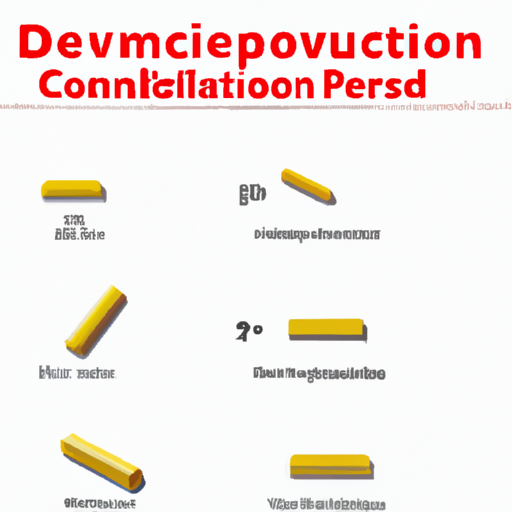
I. Introduction
A. Definition of DC Resistors
DC resistors are passive electronic components that resist the flow of direct current (DC) in a circuit. They are essential for controlling voltage and current levels, dividing voltages, and protecting sensitive components from excessive current. Resistors are characterized by their resistance value, which is measured in ohms (Ω), and they come in various types and configurations to suit different applications.
B. Importance of DC Resistors in Electronic Circuits
In electronic circuits, DC resistors play a crucial role in ensuring proper functionality. They are used in a wide range of applications, from simple circuits in household electronics to complex systems in industrial machinery. By managing current flow, resistors help maintain circuit stability, prevent damage to components, and ensure that devices operate within their specified parameters. Their reliability and performance are vital for the overall efficiency of electronic systems.
C. Overview of the Production Process
The production of DC resistors involves several key processes, from sourcing raw materials to final testing and packaging. Understanding these processes is essential for manufacturers aiming to produce high-quality resistors that meet industry standards. This blog post will explore the common production processes for DC resistors, including the types of resistors, raw materials used, fabrication techniques, and the impact of technology and environmental considerations.
II. Types of DC Resistors
A. Fixed Resistors
Fixed resistors have a constant resistance value and are the most commonly used type in electronic circuits. They can be further categorized into:
1. **Carbon Composition Resistors**: Made from a mixture of carbon and a binding material, these resistors are known for their high energy absorption and ability to withstand high temperatures.
2. **Metal Film Resistors**: These resistors are constructed by depositing a thin layer of metal onto a ceramic substrate. They offer high precision and stability, making them suitable for applications requiring accurate resistance values.
3. **Wirewound Resistors**: Composed of a wire wound around a core, these resistors can handle high power levels and are often used in power applications.
B. Variable Resistors
Variable resistors allow for adjustable resistance values, making them versatile components in electronic circuits. They include:
1. **Potentiometers**: Used for adjusting voltage levels in circuits, potentiometers are commonly found in volume controls and other adjustable settings.
2. **Rheostats**: Similar to potentiometers but designed to handle higher currents, rheostats are used in applications where variable resistance is needed.
C. Specialty Resistors
Specialty resistors are designed for specific applications and include:
1. **Precision Resistors**: These resistors have tight tolerance levels and are used in applications where accuracy is critical.
2. **High-Power Resistors**: Built to withstand high power levels, these resistors are used in industrial applications and power electronics.
III. Raw Materials Used in Resistor Production
A. Conductive Materials
The performance of resistors largely depends on the materials used in their construction. Common conductive materials include:
1. **Carbon**: Used in carbon composition resistors, carbon provides good conductivity and thermal stability.
2. **Metal Oxides**: Employed in metal film resistors, metal oxides offer high precision and stability.
3. **Metal Alloys**: Used in wirewound resistors, metal alloys provide durability and high power handling capabilities.
B. Insulating Materials
Insulating materials are crucial for ensuring the safety and reliability of resistors. Common insulating materials include:
1. **Ceramics**: Often used as substrates for resistors, ceramics provide excellent thermal and electrical insulation.
2. **Epoxy Resins**: Used for encapsulating resistors, epoxy resins protect against environmental factors and mechanical stress.
3. **Plastics**: Employed in various resistor types, plastics offer lightweight and cost-effective insulation solutions.
IV. Common Production Processes
A. Material Preparation
1. Sourcing and Quality Control
The production of DC resistors begins with sourcing high-quality raw materials. Manufacturers must establish relationships with reliable suppliers and implement stringent quality control measures to ensure that materials meet industry standards.
2. Material Processing Techniques
Once sourced, raw materials undergo processing techniques such as grinding, mixing, and shaping to prepare them for resistor fabrication. For example, carbon materials may be ground into a fine powder, while metal films are deposited onto substrates using advanced techniques.
B. Resistor Fabrication
The fabrication process varies depending on the type of resistor being produced:
1. Carbon Composition Resistors
Mixing and Molding: The carbon powder is mixed with a binding agent and molded into the desired shape.
Curing and Finishing: The molded resistors are cured to harden the material, followed by finishing processes to achieve the required resistance values.
2. Metal Film Resistors
Thin Film Deposition: A thin layer of metal is deposited onto a ceramic substrate using techniques such as sputtering or chemical vapor deposition.
Laser Trimming: The resistance value is fine-tuned using laser trimming, which removes precise amounts of the metal film.
3. Wirewound Resistors
Wire Winding: A wire is wound around a core to create the resistor element.
Insulation and Coating: The wound wire is insulated and coated to protect against environmental factors and ensure safety.
C. Assembly and Packaging
1. Mounting Techniques
After fabrication, resistors are mounted onto circuit boards using various techniques, including surface mount technology (SMT) and through-hole mounting.
2. Encapsulation and Coating
Resistors are encapsulated in protective materials to shield them from moisture, dust, and mechanical stress. This step is crucial for ensuring long-term reliability.
D. Testing and Quality Assurance
1. Electrical Testing
Each resistor undergoes electrical testing to verify its resistance value and performance characteristics. This step ensures that the resistors meet specified tolerances.
2. Environmental Testing
Resistors are subjected to environmental testing to assess their performance under various conditions, such as temperature and humidity.
3. Reliability Testing
Reliability testing evaluates the long-term performance of resistors, ensuring they can withstand the rigors of their intended applications.
V. Automation and Technology in Resistor Production
A. Role of Automation in Manufacturing
Automation plays a significant role in the production of DC resistors, enhancing efficiency and consistency. Automated systems streamline processes such as material handling, assembly, and testing, reducing the risk of human error.
B. Advances in Production Technology
Recent advancements in production technology, such as 3D printing and advanced material science, have opened new avenues for resistor design and manufacturing. These technologies enable the creation of more complex resistor structures and improved performance characteristics.
C. Impact of Industry 4.0 on Resistor Production
The integration of Industry 4.0 principles, including the Internet of Things (IoT) and data analytics, is transforming resistor production. Manufacturers can now monitor production processes in real-time, optimize operations, and enhance product quality through data-driven decision-making.
VI. Environmental Considerations
A. Sustainable Practices in Resistor Manufacturing
As environmental concerns grow, manufacturers are adopting sustainable practices in resistor production. This includes using eco-friendly materials, reducing energy consumption, and minimizing waste.
B. Waste Management and Recycling
Effective waste management strategies are essential for reducing the environmental impact of resistor production. Manufacturers are implementing recycling programs to reclaim materials and reduce landfill waste.
C. Compliance with Environmental Regulations
Compliance with environmental regulations is crucial for resistor manufacturers. Adhering to standards ensures that production processes are environmentally responsible and sustainable.
VII. Conclusion
A. Summary of Key Points
The production of DC resistors involves a complex interplay of materials, fabrication techniques, and quality assurance processes. Understanding these processes is essential for manufacturers aiming to produce reliable and high-performance resistors.
B. Future Trends in DC Resistor Production
As technology continues to evolve, the future of DC resistor production will likely see further advancements in automation, material science, and sustainable practices. Manufacturers must stay abreast of these trends to remain competitive in the market.
C. Importance of Continuous Improvement in Manufacturing Processes
Continuous improvement is vital for enhancing the quality and efficiency of resistor production. By embracing innovation and adopting best practices, manufacturers can ensure that they meet the ever-changing demands of the electronics industry.
VIII. References
A. Academic Journals
- Journal of Electronic Materials
- IEEE Transactions on Components, Packaging and Manufacturing Technology
B. Industry Reports
- Market Research Reports on Resistor Manufacturing
- Industry Analysis Reports from Electronics Associations
C. Manufacturer Guidelines
- Technical Specifications from Resistor Manufacturers
- Best Practices for Resistor Production from Industry Leaders
---
This blog post provides a comprehensive overview of the common production processes for DC resistors, highlighting the importance of these components in electronic circuits and the various factors that influence their manufacturing. By understanding these processes, manufacturers can enhance their production capabilities and contribute to the advancement of electronic technology.