What is the Common Production Process of Adjustable Resistors?
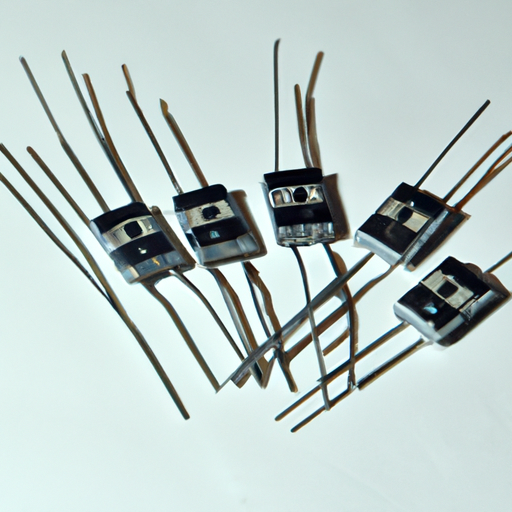
I. Introduction
Adjustable resistors, commonly known as variable resistors, are essential components in electronic circuits. They allow for the adjustment of resistance values, enabling fine-tuning of electrical signals and control over current flow. This versatility makes them invaluable in a wide range of applications, from audio equipment to industrial machinery. Understanding the production process of adjustable resistors is crucial for appreciating their role in electronics and the engineering behind their design.
II. Types of Adjustable Resistors
A. Potentiometers
Potentiometers are perhaps the most recognized type of adjustable resistor. They consist of three terminals: two connected to a resistive element and one connected to a wiper that moves along the element. This movement allows users to adjust the resistance and, consequently, the voltage output. Potentiometers are widely used in volume controls, light dimmers, and various other applications where variable voltage is required.
B. Rheostats
Rheostats are similar to potentiometers but are typically used to control higher currents. They usually have two terminals and are designed to handle larger loads. Rheostats are often found in applications such as motor speed controls and heating elements, where adjusting the current flow is necessary for performance.
C. Trimmers
Trimmers are small, adjustable resistors used for fine-tuning circuits. They are often found in printed circuit boards (PCBs) and are adjusted only during the setup phase of a device. Trimmers are crucial for calibrating devices to ensure optimal performance, making them essential in precision electronics.
III. Materials Used in Production
A. Conductive Materials
The choice of conductive materials is critical in the production of adjustable resistors. Common materials include:
1. **Carbon Composition**: This material is made from a mixture of carbon and a binding agent. It is cost-effective and provides good performance for low-power applications.
2. **Metal Film**: Metal film resistors offer better stability and accuracy than carbon composition. They are often used in applications requiring precise resistance values.
3. **Wirewound**: Wirewound resistors are made by winding a metal wire around a ceramic or plastic core. They are capable of handling high power and are used in applications where durability is essential.
B. Insulating Materials
Insulating materials are equally important in ensuring the reliability and safety of adjustable resistors. Common insulating materials include:
1. **Plastics**: Used for housings and terminals, plastics provide good insulation and are lightweight.
2. **Ceramics**: Often used in high-temperature applications, ceramics offer excellent thermal stability and electrical insulation.
C. Other Components
In addition to conductive and insulating materials, adjustable resistors require various other components, including terminals for electrical connections and housings to protect the internal components.
IV. Design and Engineering Phase
A. Conceptual Design
The production of adjustable resistors begins with a conceptual design phase. Engineers define specifications and requirements based on the intended application. This phase often involves creating prototypes to test different designs and materials.
B. Computer-Aided Design (CAD)
Once a conceptual design is established, engineers use Computer-Aided Design (CAD) software to create detailed 3D models of the adjustable resistors. CAD allows for precise modeling of the components and enables simulations of electrical properties, ensuring that the design meets performance criteria before moving to production.
V. Manufacturing Process
A. Material Preparation
The manufacturing process begins with material preparation. This includes sourcing high-quality materials and conducting quality control checks to ensure they meet industry standards. Once the materials are approved, they are cut and shaped according to the specifications outlined in the design phase.
B. Assembly Process
The assembly process involves several steps:
1. **Component Assembly**: Individual components, such as the resistive element, terminals, and housing, are assembled together. This step requires precision to ensure that all parts fit correctly.
2. **Soldering Techniques**: Soldering is used to create electrical connections between components. Various soldering techniques, including wave soldering and reflow soldering, may be employed depending on the design and materials used.
C. Calibration and Testing
After assembly, adjustable resistors undergo calibration and testing. This includes:
1. **Electrical Testing**: Each resistor is tested for its electrical properties, ensuring it meets the specified resistance values.
2. **Performance Validation**: The resistors are subjected to various performance tests to validate their functionality under different conditions.
VI. Quality Control Measures
Quality control is a critical aspect of the production process. Manufacturers implement several measures to ensure the reliability and performance of adjustable resistors:
A. In-Process Inspections
Throughout the manufacturing process, in-process inspections are conducted to identify any defects or inconsistencies. This proactive approach helps to minimize waste and ensure that only high-quality products move forward in the production line.
B. Final Product Testing
Once the adjustable resistors are fully assembled, they undergo final product testing. This includes comprehensive electrical tests and performance evaluations to ensure they meet industry standards and customer expectations.
C. Compliance with Industry Standards
Manufacturers must comply with various industry standards, such as ISO and RoHS, to ensure their products are safe and environmentally friendly. Compliance not only enhances product quality but also builds trust with customers.
VII. Packaging and Distribution
A. Packaging Techniques
Once the adjustable resistors pass quality control, they are packaged for distribution. Packaging techniques vary depending on the type of resistor and the target market. Proper packaging is essential to protect the components during transportation and storage.
B. Distribution Channels
Manufacturers utilize various distribution channels to reach their customers, including direct sales, online platforms, and partnerships with electronic component distributors. Efficient distribution is crucial for meeting market demand and ensuring timely delivery.
C. Market Considerations
Understanding market trends and customer needs is vital for manufacturers. This knowledge helps them adapt their production processes and product offerings to stay competitive in the ever-evolving electronics market.
VIII. Conclusion
The production process of adjustable resistors is a complex and multifaceted endeavor that involves careful planning, precise engineering, and stringent quality control. From the initial design phase to the final packaging and distribution, each step is crucial in ensuring that these components meet the high standards required in modern electronics.
As technology continues to advance, the manufacturing processes for adjustable resistors are likely to evolve as well. Innovations in materials, design techniques, and production methods will drive improvements in performance, reliability, and cost-effectiveness. Continuous improvement in production techniques will be essential for manufacturers to remain competitive and meet the growing demands of the electronics industry.
IX. References
1. Academic Journals on Electrical Engineering
2. Industry Reports on Electronic Components
3. Manufacturer Guidelines for Adjustable Resistors
This comprehensive overview of the common production process of adjustable resistors highlights the importance of these components in electronic circuits and the intricate steps involved in their manufacturing. Understanding this process not only enhances our appreciation for these devices but also underscores the significance of quality and innovation in the electronics industry.
What is the Common Production Process of Adjustable Resistors?
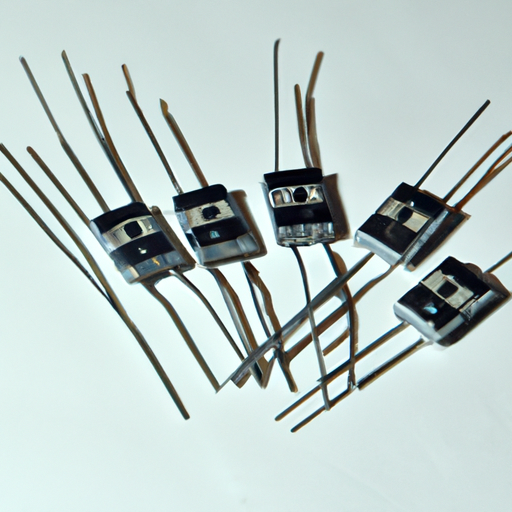
I. Introduction
Adjustable resistors, commonly known as variable resistors, are essential components in electronic circuits. They allow for the adjustment of resistance values, enabling fine-tuning of electrical signals and control over current flow. This versatility makes them invaluable in a wide range of applications, from audio equipment to industrial machinery. Understanding the production process of adjustable resistors is crucial for appreciating their role in electronics and the engineering behind their design.
II. Types of Adjustable Resistors
A. Potentiometers
Potentiometers are perhaps the most recognized type of adjustable resistor. They consist of three terminals: two connected to a resistive element and one connected to a wiper that moves along the element. This movement allows users to adjust the resistance and, consequently, the voltage output. Potentiometers are widely used in volume controls, light dimmers, and various other applications where variable voltage is required.
B. Rheostats
Rheostats are similar to potentiometers but are typically used to control higher currents. They usually have two terminals and are designed to handle larger loads. Rheostats are often found in applications such as motor speed controls and heating elements, where adjusting the current flow is necessary for performance.
C. Trimmers
Trimmers are small, adjustable resistors used for fine-tuning circuits. They are often found in printed circuit boards (PCBs) and are adjusted only during the setup phase of a device. Trimmers are crucial for calibrating devices to ensure optimal performance, making them essential in precision electronics.
III. Materials Used in Production
A. Conductive Materials
The choice of conductive materials is critical in the production of adjustable resistors. Common materials include:
1. **Carbon Composition**: This material is made from a mixture of carbon and a binding agent. It is cost-effective and provides good performance for low-power applications.
2. **Metal Film**: Metal film resistors offer better stability and accuracy than carbon composition. They are often used in applications requiring precise resistance values.
3. **Wirewound**: Wirewound resistors are made by winding a metal wire around a ceramic or plastic core. They are capable of handling high power and are used in applications where durability is essential.
B. Insulating Materials
Insulating materials are equally important in ensuring the reliability and safety of adjustable resistors. Common insulating materials include:
1. **Plastics**: Used for housings and terminals, plastics provide good insulation and are lightweight.
2. **Ceramics**: Often used in high-temperature applications, ceramics offer excellent thermal stability and electrical insulation.
C. Other Components
In addition to conductive and insulating materials, adjustable resistors require various other components, including terminals for electrical connections and housings to protect the internal components.
IV. Design and Engineering Phase
A. Conceptual Design
The production of adjustable resistors begins with a conceptual design phase. Engineers define specifications and requirements based on the intended application. This phase often involves creating prototypes to test different designs and materials.
B. Computer-Aided Design (CAD)
Once a conceptual design is established, engineers use Computer-Aided Design (CAD) software to create detailed 3D models of the adjustable resistors. CAD allows for precise modeling of the components and enables simulations of electrical properties, ensuring that the design meets performance criteria before moving to production.
V. Manufacturing Process
A. Material Preparation
The manufacturing process begins with material preparation. This includes sourcing high-quality materials and conducting quality control checks to ensure they meet industry standards. Once the materials are approved, they are cut and shaped according to the specifications outlined in the design phase.
B. Assembly Process
The assembly process involves several steps:
1. **Component Assembly**: Individual components, such as the resistive element, terminals, and housing, are assembled together. This step requires precision to ensure that all parts fit correctly.
2. **Soldering Techniques**: Soldering is used to create electrical connections between components. Various soldering techniques, including wave soldering and reflow soldering, may be employed depending on the design and materials used.
C. Calibration and Testing
After assembly, adjustable resistors undergo calibration and testing. This includes:
1. **Electrical Testing**: Each resistor is tested for its electrical properties, ensuring it meets the specified resistance values.
2. **Performance Validation**: The resistors are subjected to various performance tests to validate their functionality under different conditions.
VI. Quality Control Measures
Quality control is a critical aspect of the production process. Manufacturers implement several measures to ensure the reliability and performance of adjustable resistors:
A. In-Process Inspections
Throughout the manufacturing process, in-process inspections are conducted to identify any defects or inconsistencies. This proactive approach helps to minimize waste and ensure that only high-quality products move forward in the production line.
B. Final Product Testing
Once the adjustable resistors are fully assembled, they undergo final product testing. This includes comprehensive electrical tests and performance evaluations to ensure they meet industry standards and customer expectations.
C. Compliance with Industry Standards
Manufacturers must comply with various industry standards, such as ISO and RoHS, to ensure their products are safe and environmentally friendly. Compliance not only enhances product quality but also builds trust with customers.
VII. Packaging and Distribution
A. Packaging Techniques
Once the adjustable resistors pass quality control, they are packaged for distribution. Packaging techniques vary depending on the type of resistor and the target market. Proper packaging is essential to protect the components during transportation and storage.
B. Distribution Channels
Manufacturers utilize various distribution channels to reach their customers, including direct sales, online platforms, and partnerships with electronic component distributors. Efficient distribution is crucial for meeting market demand and ensuring timely delivery.
C. Market Considerations
Understanding market trends and customer needs is vital for manufacturers. This knowledge helps them adapt their production processes and product offerings to stay competitive in the ever-evolving electronics market.
VIII. Conclusion
The production process of adjustable resistors is a complex and multifaceted endeavor that involves careful planning, precise engineering, and stringent quality control. From the initial design phase to the final packaging and distribution, each step is crucial in ensuring that these components meet the high standards required in modern electronics.
As technology continues to advance, the manufacturing processes for adjustable resistors are likely to evolve as well. Innovations in materials, design techniques, and production methods will drive improvements in performance, reliability, and cost-effectiveness. Continuous improvement in production techniques will be essential for manufacturers to remain competitive and meet the growing demands of the electronics industry.
IX. References
1. Academic Journals on Electrical Engineering
2. Industry Reports on Electronic Components
3. Manufacturer Guidelines for Adjustable Resistors
This comprehensive overview of the common production process of adjustable resistors highlights the importance of these components in electronic circuits and the intricate steps involved in their manufacturing. Understanding this process not only enhances our appreciation for these devices but also underscores the significance of quality and innovation in the electronics industry.