Common Production Processes for Large Angles
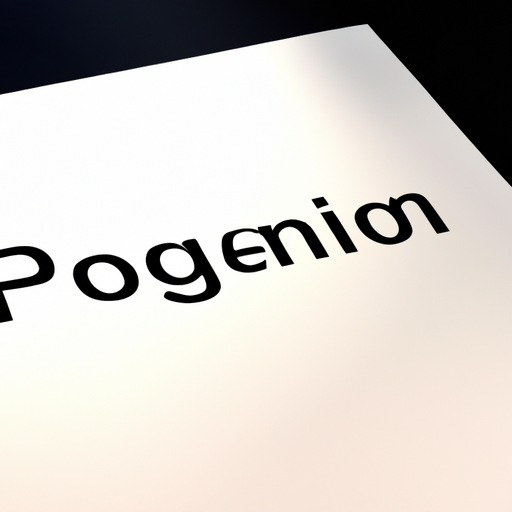
I. Introduction
In the realm of manufacturing, the term "large angles" refers to angles that exceed 90 degrees, often found in various components and structures across multiple industries. The production of these angles is critical, as they play a significant role in the functionality and integrity of products ranging from automotive parts to architectural frameworks. Precision in large angle production is paramount, as even minor deviations can lead to significant performance issues or structural failures. This article aims to explore the common production processes for large angles, highlighting their applications, challenges, and the importance of maintaining high standards of quality and precision.
II. Understanding Large Angles
A. Definition and Significance in Various Industries
Large angles are defined as angles greater than 90 degrees, and they are essential in various applications, including mechanical assemblies, structural components, and specialized tools. Industries such as aerospace, automotive, construction, and manufacturing frequently utilize large angles in their designs. For instance, in aerospace engineering, large angles are often found in wing structures and fuselage designs, where aerodynamic efficiency is crucial.
B. Applications of Large Angles in Engineering and Manufacturing
The applications of large angles are diverse. In construction, large angles are used in trusses and beams to provide stability and support. In the automotive industry, components like suspension systems and chassis often incorporate large angles to enhance performance and safety. Additionally, large angles are prevalent in machinery and equipment, where they contribute to the overall functionality and efficiency of the systems.
C. Challenges Associated with Producing Large Angles
Producing large angles presents several challenges, including the need for precise measurements, the potential for material deformation, and the complexity of the manufacturing processes involved. Achieving the desired angle while maintaining the integrity of the material can be difficult, especially when working with metals and other rigid materials. Furthermore, the production processes must be carefully selected to ensure that the final product meets the required specifications.
III. Common Production Processes for Large Angles
A. Machining Processes
1. CNC Machining
CNC (Computer Numerical Control) machining is a highly precise manufacturing process that utilizes computer-controlled machines to create complex shapes and angles. This technology is particularly advantageous for large angle production, as it allows for high levels of accuracy and repeatability. CNC machines can be programmed to produce large angles with tight tolerances, making them ideal for applications where precision is critical.
2. Milling
Milling is another common machining process used to create large angles. Various types of milling machines, such as vertical and horizontal mills, can be employed to achieve the desired angle. Techniques such as angular milling and face milling are often used to produce large angles, allowing manufacturers to create intricate designs with high precision.
3. Turning
Turning is a machining process that involves rotating a workpiece against a cutting tool to create cylindrical shapes. This process can also be adapted to produce large angles, particularly in components that require a combination of cylindrical and angular features. Turning is commonly used in the production of shafts, fittings, and other components where large angles are necessary.
B. Fabrication Processes
1. Welding
Welding is a fabrication process that joins materials together by melting and fusing them. Various types of welding, such as MIG (Metal Inert Gas) and TIG (Tungsten Inert Gas), are suitable for large angle production. The design and preparation of joints are crucial in this process, as they directly impact the strength and integrity of the final product. Proper joint design can help mitigate issues related to distortion and misalignment.
2. Bending
Bending is a process used to create large angles by deforming materials along a predetermined line. Methods such as air bending, bottoming, and coining can be employed to achieve the desired angle. Equipment like press brakes and tube benders are commonly used in this process. The choice of bending method depends on the material type, thickness, and the specific angle required.
3. Forming
Forming techniques, such as stamping and forging, can also be utilized to produce large angles. These processes involve shaping materials through the application of force, allowing manufacturers to create complex geometries with high precision. Considerations for large angle forming include material properties, tooling design, and the potential for springback, which can affect the final angle.
C. Casting and Molding
1. Investment Casting
Investment casting is a process that involves creating a wax pattern, coating it with a ceramic shell, and then melting the wax away to create a mold. This method is particularly beneficial for producing large angle components with intricate designs and high dimensional accuracy. Investment casting is widely used in industries such as aerospace and automotive, where precision is critical.
2. Die Casting
Die casting is a manufacturing process that involves forcing molten metal into a mold under high pressure. This method is suitable for producing large angle components with excellent surface finishes and dimensional accuracy. Die casting is commonly used for aluminum and zinc alloys, making it ideal for applications in the automotive and electronics industries.
3. Injection Molding
Injection molding is a process used to create plastic components by injecting molten plastic into a mold. This method is increasingly being used to produce large angles in plastic materials, particularly in consumer products and industrial applications. The versatility of injection molding allows for the production of complex shapes and angles with high precision.
D. Additive Manufacturing
1. Overview of 3D Printing Technologies
Additive manufacturing, commonly known as 3D printing, is an innovative production process that builds components layer by layer. This technology has gained popularity for its ability to create complex geometries, including large angles, with minimal material waste. Various 3D printing technologies, such as FDM (Fused Deposition Modeling) and SLA (Stereolithography), can be employed to produce large angle components.
2. Advantages of Additive Manufacturing for Large Angles
One of the primary advantages of additive manufacturing is its design flexibility, allowing for the creation of intricate shapes that may be challenging to achieve with traditional manufacturing methods. Additionally, 3D printing can significantly reduce lead times and costs, making it an attractive option for prototyping and low-volume production of large angle components.
3. Limitations and Considerations
Despite its advantages, additive manufacturing also has limitations. The mechanical properties of 3D-printed components may not always match those produced through traditional methods, and considerations such as layer adhesion and surface finish must be taken into account. Furthermore, the choice of materials for 3D printing can impact the performance of large angle components.
IV. Quality Control and Precision Measurement
A. Importance of Quality Control in Large Angle Production
Quality control is essential in large angle production to ensure that components meet the required specifications and performance standards. Implementing rigorous quality control measures helps identify defects early in the manufacturing process, reducing the risk of costly rework and ensuring the reliability of the final product.
B. Techniques for Measuring Large Angles
Accurate measurement of large angles is critical for maintaining precision in production. Various techniques can be employed, including:
1. Goniometers
Goniometers are specialized instruments used to measure angles with high precision. They are commonly used in laboratories and manufacturing settings to ensure that large angles meet the required specifications.
2. Laser Measurement Systems
Laser measurement systems offer a non-contact method for measuring angles and distances with high accuracy. These systems are particularly useful in large-scale manufacturing environments, where traditional measurement methods may be impractical.
C. Ensuring Precision and Accuracy in Production
To ensure precision and accuracy in large angle production, manufacturers must implement robust quality control processes, utilize advanced measurement techniques, and continuously monitor production processes. Regular calibration of equipment and adherence to industry standards are also crucial for maintaining high levels of precision.
V. Conclusion
In summary, the production of large angles is a complex process that involves various machining, fabrication, casting, molding, and additive manufacturing techniques. Each method has its advantages and challenges, and the choice of process depends on factors such as material type, design complexity, and required precision. As industries continue to evolve, the demand for high-quality large angle components will only increase, making precision in production processes more critical than ever. Future trends in large angle manufacturing may include advancements in automation, improved materials, and innovative production techniques, all aimed at enhancing efficiency and accuracy. Ultimately, the importance of precision in large angle production cannot be overstated, as it directly impacts the performance and reliability of the final products across various industries.
Common Production Processes for Large Angles
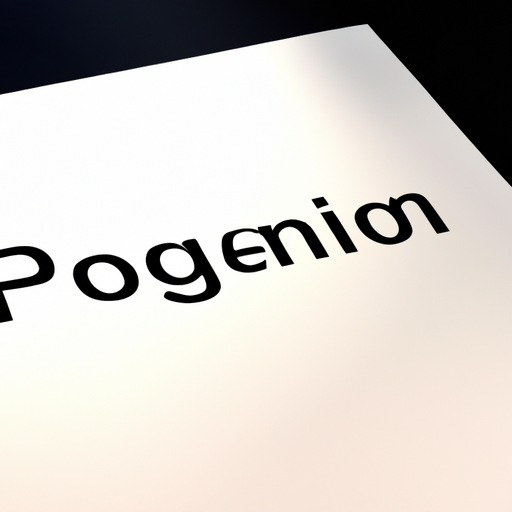
I. Introduction
In the realm of manufacturing, the term "large angles" refers to angles that exceed 90 degrees, often found in various components and structures across multiple industries. The production of these angles is critical, as they play a significant role in the functionality and integrity of products ranging from automotive parts to architectural frameworks. Precision in large angle production is paramount, as even minor deviations can lead to significant performance issues or structural failures. This article aims to explore the common production processes for large angles, highlighting their applications, challenges, and the importance of maintaining high standards of quality and precision.
II. Understanding Large Angles
A. Definition and Significance in Various Industries
Large angles are defined as angles greater than 90 degrees, and they are essential in various applications, including mechanical assemblies, structural components, and specialized tools. Industries such as aerospace, automotive, construction, and manufacturing frequently utilize large angles in their designs. For instance, in aerospace engineering, large angles are often found in wing structures and fuselage designs, where aerodynamic efficiency is crucial.
B. Applications of Large Angles in Engineering and Manufacturing
The applications of large angles are diverse. In construction, large angles are used in trusses and beams to provide stability and support. In the automotive industry, components like suspension systems and chassis often incorporate large angles to enhance performance and safety. Additionally, large angles are prevalent in machinery and equipment, where they contribute to the overall functionality and efficiency of the systems.
C. Challenges Associated with Producing Large Angles
Producing large angles presents several challenges, including the need for precise measurements, the potential for material deformation, and the complexity of the manufacturing processes involved. Achieving the desired angle while maintaining the integrity of the material can be difficult, especially when working with metals and other rigid materials. Furthermore, the production processes must be carefully selected to ensure that the final product meets the required specifications.
III. Common Production Processes for Large Angles
A. Machining Processes
1. CNC Machining
CNC (Computer Numerical Control) machining is a highly precise manufacturing process that utilizes computer-controlled machines to create complex shapes and angles. This technology is particularly advantageous for large angle production, as it allows for high levels of accuracy and repeatability. CNC machines can be programmed to produce large angles with tight tolerances, making them ideal for applications where precision is critical.
2. Milling
Milling is another common machining process used to create large angles. Various types of milling machines, such as vertical and horizontal mills, can be employed to achieve the desired angle. Techniques such as angular milling and face milling are often used to produce large angles, allowing manufacturers to create intricate designs with high precision.
3. Turning
Turning is a machining process that involves rotating a workpiece against a cutting tool to create cylindrical shapes. This process can also be adapted to produce large angles, particularly in components that require a combination of cylindrical and angular features. Turning is commonly used in the production of shafts, fittings, and other components where large angles are necessary.
B. Fabrication Processes
1. Welding
Welding is a fabrication process that joins materials together by melting and fusing them. Various types of welding, such as MIG (Metal Inert Gas) and TIG (Tungsten Inert Gas), are suitable for large angle production. The design and preparation of joints are crucial in this process, as they directly impact the strength and integrity of the final product. Proper joint design can help mitigate issues related to distortion and misalignment.
2. Bending
Bending is a process used to create large angles by deforming materials along a predetermined line. Methods such as air bending, bottoming, and coining can be employed to achieve the desired angle. Equipment like press brakes and tube benders are commonly used in this process. The choice of bending method depends on the material type, thickness, and the specific angle required.
3. Forming
Forming techniques, such as stamping and forging, can also be utilized to produce large angles. These processes involve shaping materials through the application of force, allowing manufacturers to create complex geometries with high precision. Considerations for large angle forming include material properties, tooling design, and the potential for springback, which can affect the final angle.
C. Casting and Molding
1. Investment Casting
Investment casting is a process that involves creating a wax pattern, coating it with a ceramic shell, and then melting the wax away to create a mold. This method is particularly beneficial for producing large angle components with intricate designs and high dimensional accuracy. Investment casting is widely used in industries such as aerospace and automotive, where precision is critical.
2. Die Casting
Die casting is a manufacturing process that involves forcing molten metal into a mold under high pressure. This method is suitable for producing large angle components with excellent surface finishes and dimensional accuracy. Die casting is commonly used for aluminum and zinc alloys, making it ideal for applications in the automotive and electronics industries.
3. Injection Molding
Injection molding is a process used to create plastic components by injecting molten plastic into a mold. This method is increasingly being used to produce large angles in plastic materials, particularly in consumer products and industrial applications. The versatility of injection molding allows for the production of complex shapes and angles with high precision.
D. Additive Manufacturing
1. Overview of 3D Printing Technologies
Additive manufacturing, commonly known as 3D printing, is an innovative production process that builds components layer by layer. This technology has gained popularity for its ability to create complex geometries, including large angles, with minimal material waste. Various 3D printing technologies, such as FDM (Fused Deposition Modeling) and SLA (Stereolithography), can be employed to produce large angle components.
2. Advantages of Additive Manufacturing for Large Angles
One of the primary advantages of additive manufacturing is its design flexibility, allowing for the creation of intricate shapes that may be challenging to achieve with traditional manufacturing methods. Additionally, 3D printing can significantly reduce lead times and costs, making it an attractive option for prototyping and low-volume production of large angle components.
3. Limitations and Considerations
Despite its advantages, additive manufacturing also has limitations. The mechanical properties of 3D-printed components may not always match those produced through traditional methods, and considerations such as layer adhesion and surface finish must be taken into account. Furthermore, the choice of materials for 3D printing can impact the performance of large angle components.
IV. Quality Control and Precision Measurement
A. Importance of Quality Control in Large Angle Production
Quality control is essential in large angle production to ensure that components meet the required specifications and performance standards. Implementing rigorous quality control measures helps identify defects early in the manufacturing process, reducing the risk of costly rework and ensuring the reliability of the final product.
B. Techniques for Measuring Large Angles
Accurate measurement of large angles is critical for maintaining precision in production. Various techniques can be employed, including:
1. Goniometers
Goniometers are specialized instruments used to measure angles with high precision. They are commonly used in laboratories and manufacturing settings to ensure that large angles meet the required specifications.
2. Laser Measurement Systems
Laser measurement systems offer a non-contact method for measuring angles and distances with high accuracy. These systems are particularly useful in large-scale manufacturing environments, where traditional measurement methods may be impractical.
C. Ensuring Precision and Accuracy in Production
To ensure precision and accuracy in large angle production, manufacturers must implement robust quality control processes, utilize advanced measurement techniques, and continuously monitor production processes. Regular calibration of equipment and adherence to industry standards are also crucial for maintaining high levels of precision.
V. Conclusion
In summary, the production of large angles is a complex process that involves various machining, fabrication, casting, molding, and additive manufacturing techniques. Each method has its advantages and challenges, and the choice of process depends on factors such as material type, design complexity, and required precision. As industries continue to evolve, the demand for high-quality large angle components will only increase, making precision in production processes more critical than ever. Future trends in large angle manufacturing may include advancements in automation, improved materials, and innovative production techniques, all aimed at enhancing efficiency and accuracy. Ultimately, the importance of precision in large angle production cannot be overstated, as it directly impacts the performance and reliability of the final products across various industries.